一、产品概述
垃圾焚烧二噁英处理系统聚焦焚烧过程中产生的二噁英类污染物(PCDD/Fs),通过 “源头抑制 – 过程控制 – 末端净化” 技术链,实现排放浓度≤0.1ng TEQ/m³(满足国标 GB 18485-2020 及欧盟严苛标准)。设备适配 300-2000t/d 焚烧规模,集成活性炭吸附、布袋除尘、SCR 催化还原等技术,同步处理飞灰、酸性气体及 NOx,为城市生活垃圾焚烧厂、工业固废焚烧炉提供多污染物协同治理方案,具备从焚烧工况优化到尾气深度净化的一体化控制能力。
二、处理原理
二噁英主要在 300-500℃低温段通过前驱物与金属催化反应生成,处理系统通过三大机制切断污染链条:
源头抑制:通过 “3T+E” 原则(燃烧室温度≥850℃、停留时间≥2 秒、过量空气系数≥1.6)确保二噁英完全分解,预处理含氯垃圾减少金属催化作用;
过程控制:急冷塔以≥100℃/s 速率将烟气从 850℃骤降至 200℃以下,跳过再合成窗口,同时喷入高活性活性炭(比表面积≥1500m²/g)吸附气相二噁英(效率≥95%);
末端净化:布袋除尘器利用活性炭 – 飞灰滤饼二次吸附,拦截≥1μm 颗粒物(去除率≥99.9%),高浓度场景配置 SCR 反应器,在 250-400℃下催化氧化二噁英(分解效率≥90%)。
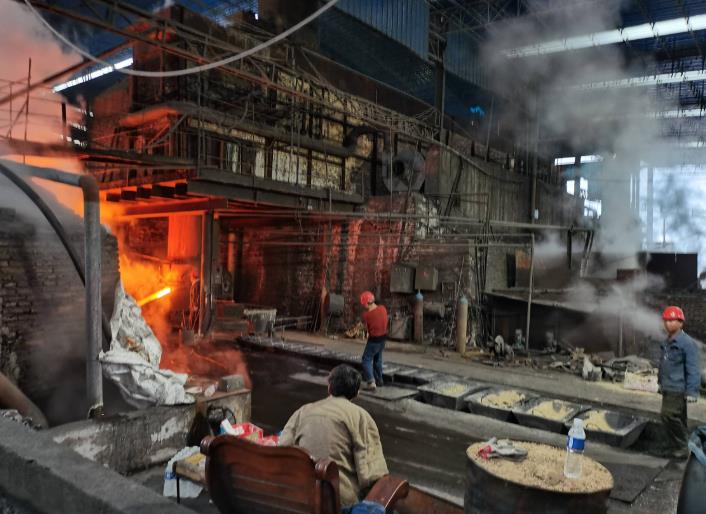
三、处理流程
治理流程贯穿焚烧前、中、后全环节:
预处理阶段:筛分去除金属杂质及大块含氯废物,破碎至≤10cm 确保燃烧充分,制备 5-10% 石灰浆用于酸性气体中和;
焚烧控制阶段:燃烧室维持 850-1100℃高温,DCS 系统监控氧量(8-12%)与停留时间,急冷塔雾化降温至 180℃以下(1 秒内完成),控制出口湿度 10-15%;
尾气净化阶段:一级喷入活性炭(5-20mg/m³)与 Ca (OH)₂粉末,吸附二噁英并中和酸性气体(去除率≥90%);二级布袋除尘滤后二噁英≤0.5ng TEQ/m³;三级 SCR 系统投用 NH₃还原剂,同步去除 NOx(效率≥85%),最终排放≤0.1ng TEQ/m³;
副产物处理:飞灰经稳定化处理(二噁英≤3μg TEQ/kg)后安全填埋,废活性炭与催化剂按危废管理,委托专业机构处置。
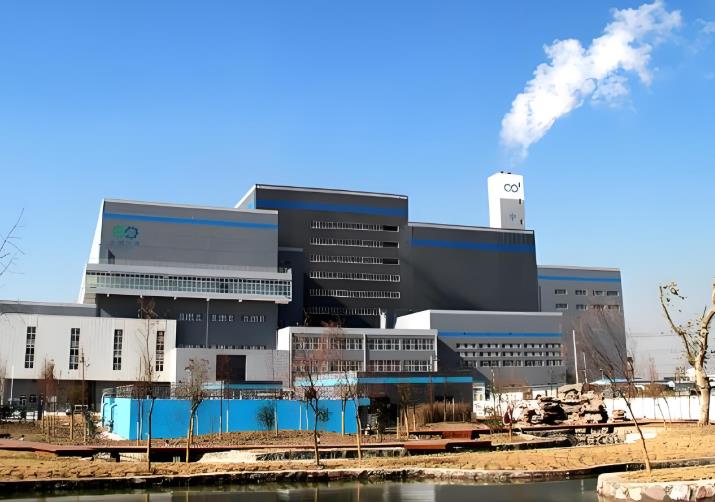
四、设备选型
选型需结合焚烧规模、合规要求与经济性:
规模适配:小型焚烧炉(≤500t/d)采用 “急冷塔 + 活性炭喷射 + 布袋除尘”(投资 15-20 万元 / 吨处理量),适合初始浓度≤5ng TEQ/m³;大型焚烧厂(≥1000t/d)配置 “急冷塔 + 活性炭吸附塔 + SCR”,处理效率≥99%,适应高氯高 NOx 工况;
合规保障:按地方限值预留 20% 处理冗余(如设计排放≤0.08ng TEQ/m³),出口项目需配高精度在线监测仪(检测精度≤0.01ng TEQ/m³);
经济运维:急冷塔采用 “空气 + 水” 复合冷却节能 30%,SCR 选用耐砷催化剂(寿命 3-5 年),活性炭优选碘值≥900mg/g 煤质炭(用量减少 20%);
安全设计:活性炭罐设防爆泄压装置(爆破片压力≤0.2MPa),管道防静电接地(电阻≤10Ω),SCR 入口设气流均布装置(流速偏差≤±5%)防止催化剂失效。